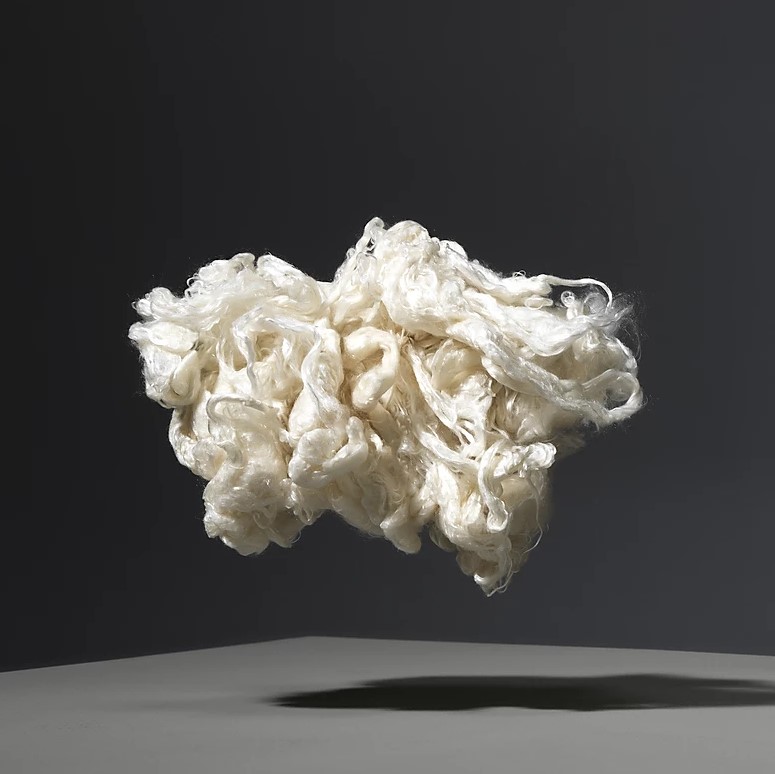
Re:newcell
There is a way to turn used cotton and viscose into new high quality biodegradable pulp, new fibers, new yarn, new fabrics and new garments that can be produced and worn with a clear conscience.
The re:newcell pulp is:
1. Circular (upcycling solution, closed loop)
2. Biodegradeable (pure cellulosic based)
3. Quality (top fiber properties)
4. Scalable (first plant already built)
Initially they prefer to recycle cotton, especially denim jeans.
They are:
1. Easy to sort (everyone can spot a pair of blue jeans).
2. They usually are close to 100% cotton.
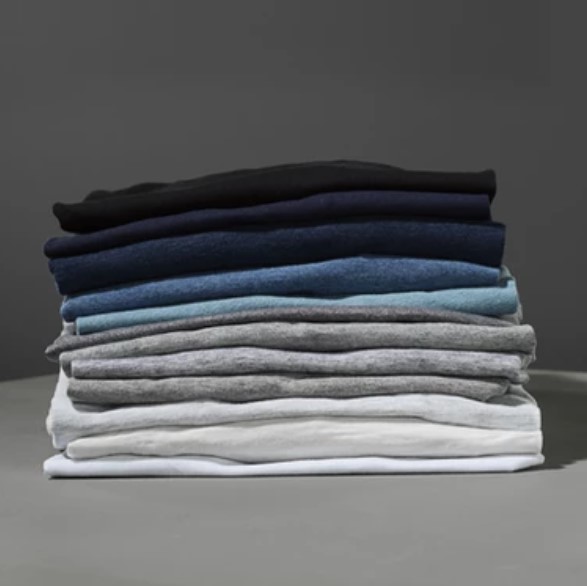
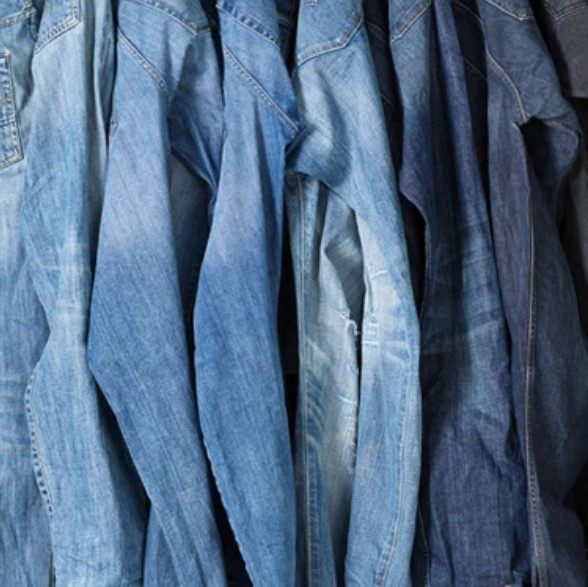
Their recycling technology dissolves used cotton and other natural fibers into a new, biodegradable raw material, re:newcell pulp.
It can be turned into textile fiber, be fed into the textile production cycle and meet industry specifications.
It’s the link that has been missing from the cycle. Fashion can finally be produced and consumed in a never-ending loop.
The very first plant opened in Sweden in 2017. It’s a demo plant with the capacity to produce 7,000 tons of re:newcell pulp every year. Energy used in the plant is only renewable energy.
The region has a long tradition in cellulosic production, they have a know-how as well as resources.
“Fashion brands are catching up to a shift in consumer demand towards sustainable raw materials. That demand pull is now finally cascading back in the value chain to the fiber producers that we’re talking to” Mr. Jonsson, CEO at re:newcell.
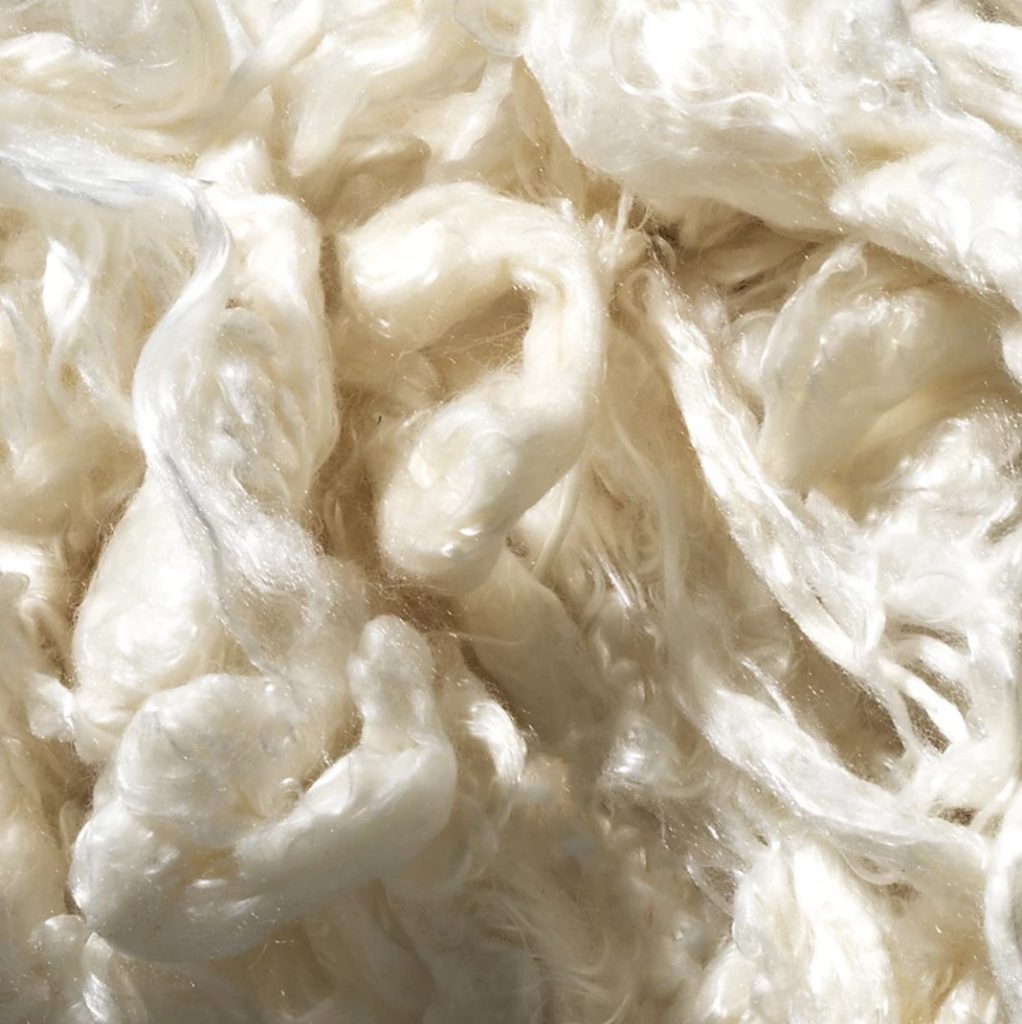
re:newcell only works with fashion brands and textile producers with a sincere desire to make fashion sustainable. No green-washing, please. These include small, high quality brands centered around sustainability, as well as larger companies committed to making a radical change towards a circular sustainable business model.